The world of hydraulic systems is vast and intricate, and when it comes to high-pressure hydraulic hoses, understanding their importance and nuances is essential for both novice and seasoned professionals. This article will delve into the specifics of hydraulic hoses designed for high-pressure applications, focusing on their critical role in ensuring system efficiency and safety.
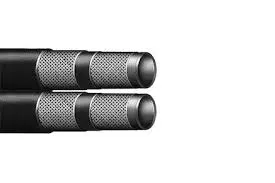
High-pressure hydraulic hoses are integral components in the transmission of force within hydraulic systems. Their primary purpose is to convey pressurized fluids for powering various mechanical components. The construction of these hoses involves a combination of robust materials, including synthetic rubber, reinforced with layers of braided or spiral steel wire to withstand the high pressures they encounter. Choosing the right hydraulic hose for high-pressure applications is crucial, as even minor discrepancies can lead to system inefficiencies or, worse, catastrophic failures.
When it comes to expertise, understanding the operating requirements of a hydraulic system is paramount. High-pressure hoses are subjected to significant stress, and selecting the appropriate hose requires a comprehensive assessment of the pressure rating, bend radius, fluid compatibility, and temperature range. For instance, a hose designed for transportation machinery might not be suitable for industrial manufacturing equipment due to differences in operating environments and pressure demands.
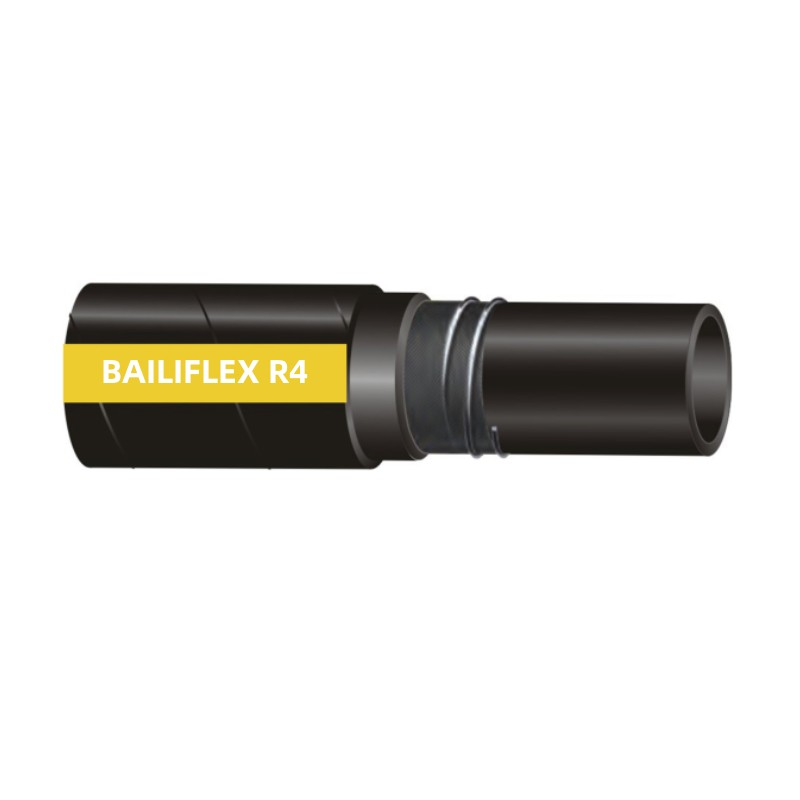
Installation of high-pressure hydraulic hoses demands a thorough understanding of system dynamics, as improper installation can lead to premature wear or failure. Experts recommend adhering to the manufacturer’s guidelines and industry standards (such as ISO or SAE) to ensure longevity and performance. Utilizing the correct fittings and adapters is also critical to maintaining the integrity of the hose assembly.
hydraulic hose high pressure
From an authoritative perspective, industry standards and certifications play a pivotal role in the reliability of hydraulic hoses. Recognized entities such as the Society of Automotive Engineers (SAE) and the International Organization for Standardization (ISO) set stringent guidelines and performance metrics to ensure the quality and safety of hydraulic hoses used in high-pressure applications. Compliance with these standards is a testament to a manufacturer’s commitment to producing durable and reliable products.
Moreover, the trustworthiness of a hydraulic hose manufacturer is often reflected in their investment in research and development. Leading manufacturers continually innovate to enhance the performance characteristics of high-pressure hoses. These innovations include advancements in materials that improve abrasion resistance and longevity, as well as the development of hose technologies that can withstand extreme environmental conditions and dynamic operational stresses.
Real-world experiences highlight the importance of regular maintenance and inspection of hydraulic hoses. Scheduled inspections are essential to detect wear and tear, misalignments, and potential leaks. Regular maintenance not only extends the lifespan of the hose but also enhances the overall performance and safety of the hydraulic system. Utilizing diagnostic tools to monitor pressure and flow rates can provide valuable insights into the condition of the hoses and preempt potential failures.
In conclusion,
hydraulic hoses designed for high-pressure applications are indispensable components of modern hydraulic systems. Their role in facilitating the efficient and safe transfer of hydraulic energy cannot be overstated. By prioritizing quality, adhering to industry standards, and investing in regular maintenance, industries can maximize the performance and safety of their hydraulic systems. As technology and materials continue to evolve, so too will the capabilities of high-pressure hydraulic hoses, ensuring their pivotal role in powering the machinery and systems that drive our world.