In the ever-evolving landscape of industrial applications, the role of metal hoses has gained increasing prominence. With unmatched flexibility and robust durability, metal hoses serve as the backbone of connectivity across numerous sectors, from petrochemical industries to high-tech manufacturing units. This article dives deep into the experience and expertise associated with metal hoses, categorically solidifying their authoritative and trustworthy status in the modern industrial toolkit.
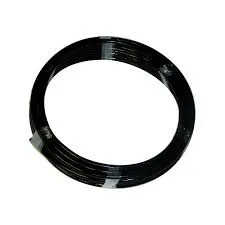
The inherent design of metal hoses allows for exceptional versatility. The intricate structure, typically composed of high-grade stainless steel, can withstand severe environmental conditions, such as extreme temperatures and high pressure. This unmatched capability fosters adaptability across various settings, whether it's an oil refinery faced with volatile chemicals or an aerospace application grappling with thermal dynamics. The longevity and resilience of these hoses not only minimize operational disruptions but also provide a cost-efficient solution, reducing the need for frequent replacements.
Drawing upon decades of engineering advancements, modern metal hoses exhibit a seamless blend of functionality and innovation. Through meticulous manufacturing processes, these hoses are crafted to meet stringent safety standards, ensuring that they perform optimally under critically demanding circumstances. An essential trait that experts look for in a premium metal hose is its corrugated design, which enhances flexibility while maintaining structural integrity. This design characteristic is pivotal, especially when navigating complex installations where spatial constraints are prevalent.
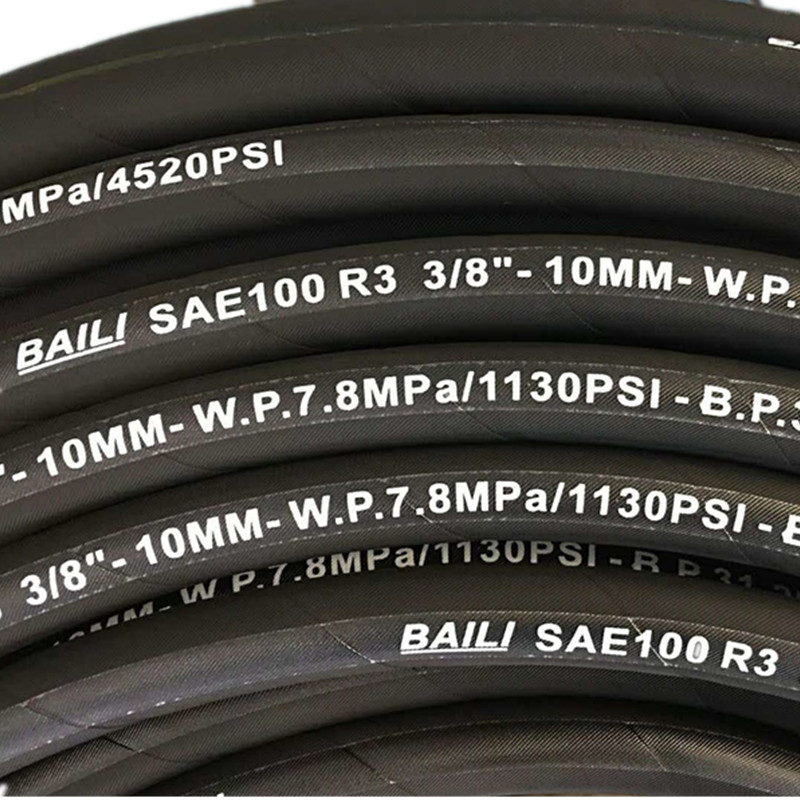
The authoritative presence of metal hoses in the industry is further solidified by strong endorsements from regulatory bodies. These hoses comply with rigorous quality benchmarks such as ISO 10380 and ASME B31.3, instilling confidence in their performance and safety metrics. Manufacturers often embark on exhaustive testing regimens, including pulsation tests and pressure cycling, to guarantee that the metal hoses remain robust over extended periods.
metal hose
Expertise in metal hose application is evident in the broad spectrum of customization options available. Tailoring the material composition and fittings to suit specific industrial needs is commonplace, ensuring maximum compatibility and efficiency. For instance, in situations where corrosive media are involved, engineers might opt for a hose with a Teflon liner to augment chemical resistance.
Similarly, for high-pressure operations, reinforced braiding might be incorporated to fortify the hose's strength.
The trustworthiness of metal hoses is not merely a product of their mechanical attributes but also of the extensive certifications and customer testimonials supporting them. Case studies often highlight the remarkable performance of metal hoses in preventing leakages and maintaining operational continuity. Industries have reported substantial returns on investment by switching to metal hoses, attributing improved productivity and reduced maintenance costs to their reliability.
In summary, metal hoses represent a critical innovation in industrial connectivity, defined by their experience-driven design and expert engineering. Their authoritative role is backed by robust industry standards and a track record of trustworthy performance. Whether managing fluid transfer in a chemical plant or accommodating thermal expansion in a high-pressure steam system, metal hoses stand out as a paradigm of dependability in industrial operations. The continued evolution of their design and material science promises even greater contributions to industry efficiency and safety in the future.