Rubber hoses, an integral component across various industries, embody resilience and flexibility—attributes critical for effectively addressing demanding applications. These versatile conduits play a pivotal role in multiple sectors, including automotive, industrial manufacturing, and even food and beverage processing. The robust design, predominantly crafted from natural or synthetic rubber, permits these hoses to transport fluids, gases, and granular substances efficiently and safely.
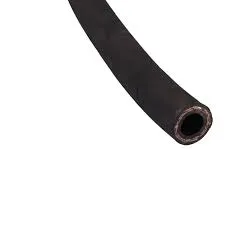
In automotive engineering, the reliability of rubber hoses is indispensable. They function as essential connectors in vehicle cooling systems, brake systems, and fuel lines, ensuring that these crucial mechanisms operate smoothly. The ability of rubber hoses to withstand high temperatures and pressures preserves engine performance, eliminating concerns over leaks or ruptures. This reliability is a testament to their engineered resilience in environments subject to intense thermal and mechanical stress.
Industrial applications further showcase the adaptability of rubber hoses. In complex machinery, hoses convey compressed air, hydraulic fluids, or chemicals critical to production processes. With specific designs tailored for abrasion resistance, chemical compatibility, and temperature endurance, they ensure the seamless operation and durability of heavy-duty equipment. The longevity of rubber hoses in such settings minimizes breakdowns, ensuring continuous productivity and enhancing operational efficiency.
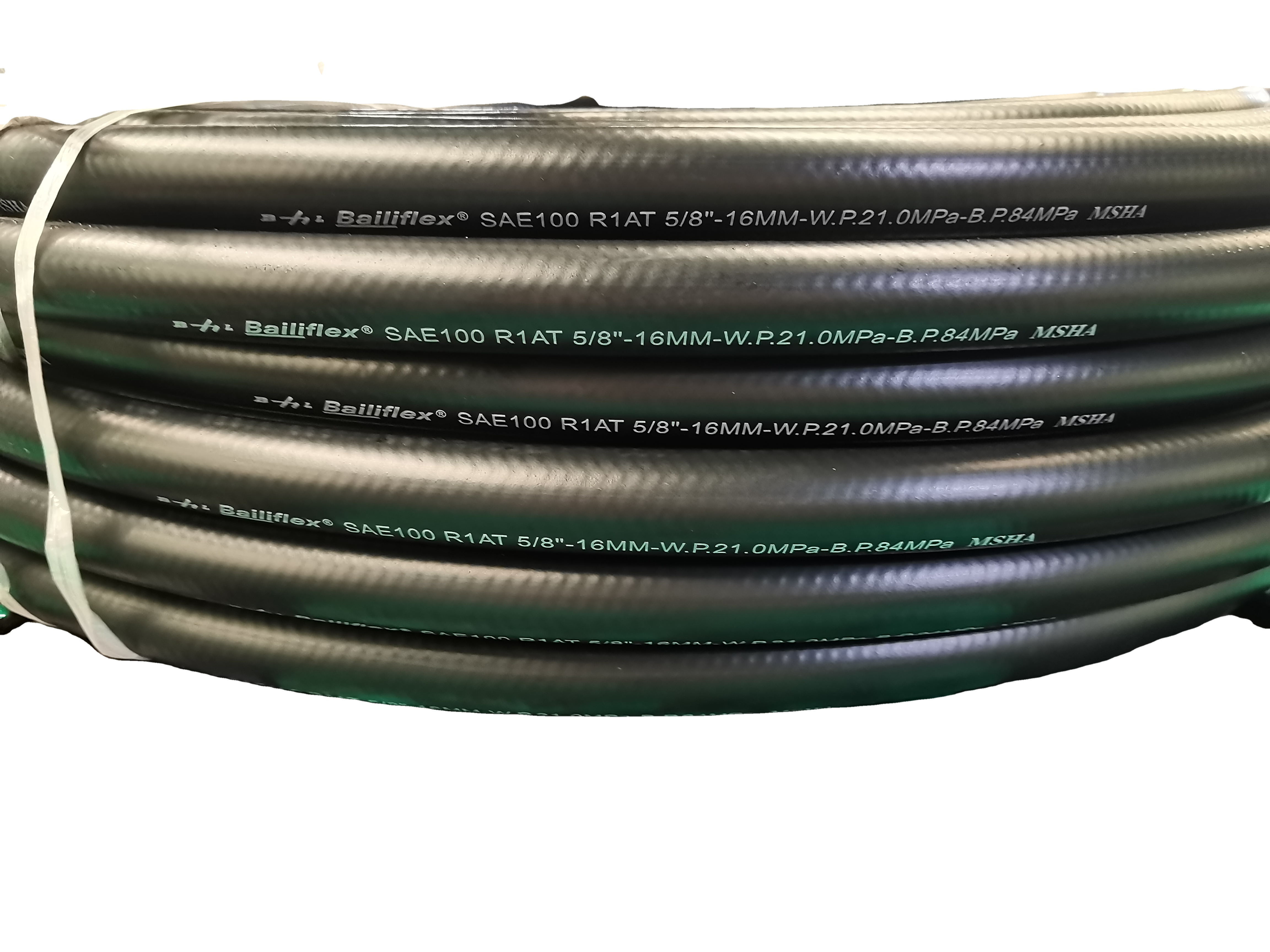
In the realm of food and beverage production, rubber hoses must meet stringent health and safety standards. Here, food-grade rubber hoses are employed to transport consumable liquids, guaranteeing purity and hygiene. These hoses are constructed to resist bacterial growth and withstand rigorous cleaning processes, underscoring their role in maintaining product integrity. The safety and compliance of these hoses with food industry standards reinforce their trustworthy application in handling consumable goods.
rubber hose
Specialized rubber compounds further expand the applicability of these hoses. The development of hoses made from EPDM (ethylene propylene diene monomer) rubber, for instance, has unlocked new potentials. Resistant to ozone, weathering, and aging, EPDM hoses are ideal for outdoor applications and use in contexts where environmental factors pose a risk. Their adaptability extends to the conveyance of hot and cold liquids, marking them as an asset in sectors where temperature fluctuations are a norm.
The expertise required to select the right rubber hose for a specific application cannot be overstated. Professionals in the field must consider various factors, including pressure ratings, temperature ranges, and environmental conditions. Consulting with manufacturers who provide authoritative guidance ensures that the chosen solution integrates seamlessly with the intended application, delivering both efficacy and reliability. Trust in such expert advice guarantees that systems incorporating rubber hoses benefit from sustained performance and safety.
In conclusion, the multifaceted role of rubber hoses across diverse industries highlights their significance as a product class. They contribute to the safe, efficient, and reliable operation of systems, illustrating the importance of selecting appropriate hoses tailored to specific operational demands. As technological advancements continue to refine their design and material composition, rubber hoses will undoubtedly remain a cornerstone of industrial and commercial applications, reflecting their unparalleled utility and trustworthiness in facilitating critical processes.