Understanding the intricacies of high pressure hydraulic hoses is crucial for anyone involved in industries that rely on these vital components, including construction, manufacturing, and heavy-duty transportation. Selecting the best high pressure hydraulic hose is not merely about browsing through options; it requires a detailed understanding of several critical factors that determine the hose's performance and longevity under extreme conditions.

High pressure hydraulic hoses are designed to withstand intense pressures and challenging environments, making them indispensable in hydraulic systems that power heavy machinery. A key consideration when choosing a hydraulic hose is its pressure rating, which must align with the hydraulic system's operating pressure.
This ensures the safety and efficiency of the machinery. A common mistake is selecting hoses with insufficient pressure ratings, leading to potential system failures. Therefore, expert knowledge of pressure specifications is paramount.
Material composition is another critical component. The ideal hydraulic hose is typically constructed from a blend of synthetic rubber, thermoplastic, or Teflon, reinforced with wire or textile braiding. Each material has unique properties that influence the hose’s flexibility, durability, and thermal resistance. For instance, hoses with stainless steel reinforcements offer superior durability and can handle higher pressure ranges, while those made of thermoplastic materials excel in environments requiring exceptional chemical resistance.
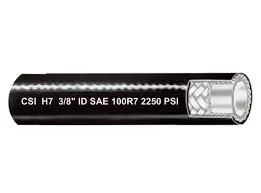
The importance of compatibility cannot be overstated. Each hydraulic system has unique specifications dictated by the machinery it supports. It’s crucial that the hose is compatible with the hydraulic fluid used, whether it be petroleum-based, synthetic, or water-based fluids. Incompatibility might result in the degradation of the hose material, leading to leakages or catastrophic failures.
Length and diameter are additional logistical factors engineers must consider. These dimensions affect the fluid flow rate and pressure regulation within the system. Additionally, the hose’s exterior must be robust enough to withstand environmental factors such as high temperatures, UV radiation, and abrasive conditions while maintaining flexibility. It’s this balance that often distinguishes superior hoses from their counterparts.
best high pressure hydraulic hose
Installation and maintenance are just as critical. Incorrect installation can undermine even the highest quality hoses, leading to performance issues. It is advisable to follow manufacturer guidelines carefully, paying close attention to the bending radius, as excessive bending can compromise hose integrity. Regular maintenance checks are essential to identify signs of wear and tear, such as cracking or bulging, which could escalate into major failures if neglected.
Authoritativeness in hydraulic systems can be gleaned from industry certifications and adherence to international standards such as ISO or SAE. Products that meet these certifications have been rigorously tested to ensure quality and reliability, providing peace of mind that they will perform as intended in demanding conditions.
In today’s high-stakes operational environments, trustworthiness translates to safety and efficiency. Opting for reputable brands known for their extensive testing, innovation, and expert engineering can save businesses from unnecessary downtime and costly repairs.
Ultimately, choosing the best high pressure hydraulic hose involves more than a superficial evaluation; it demands a comprehensive understanding of technical specifications, material science, and application-specific requirements. Consulting industry experts and leveraging resources like engineering manuals can significantly enhance decision-making processes. Only through such informed choices can companies ensure the seamless and safe operation of their hydraulic systems, safeguarding both their workforce and their bottom line.