Braided rubber hoses are a pivotal component in various industrial and domestic applications. They combine flexibility, durability, and the ability to withstand pressure, making them indispensable for both professional engineers and home mechanics. This intricate blend of rubber and braided fibers, often made from synthetic materials like nylon or polyester, offers enhanced performance characteristics over traditional hoses.
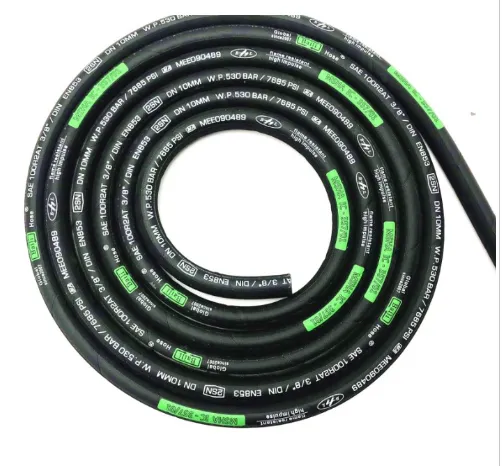
One of the standout benefits of braided rubber hoses is their exceptional pressure resistance. This is due to the braided layer that reinforces the rubber, allowing it to handle significantly higher pressures without compromising its structural integrity. For industries like automotive and aerospace, where fluid dynamics are crucial, the introduction of a braided layer ensures that hoses can cope with dynamic pressures, reducing the risk of ruptures or leaks that could lead to catastrophic failures.
Another essential attribute of braided rubber hoses is flexibility. Despite their robust construction, these hoses maintain a high degree of pliability, which is critical in applications where they need to maneuver through tight spaces or around obstacles. This flexibility does not come at the cost of performance. The braided reinforcement provides the required robustness to maintain function under stress, making them ideal for environments where both movement and high-pressure flow are commonplace.
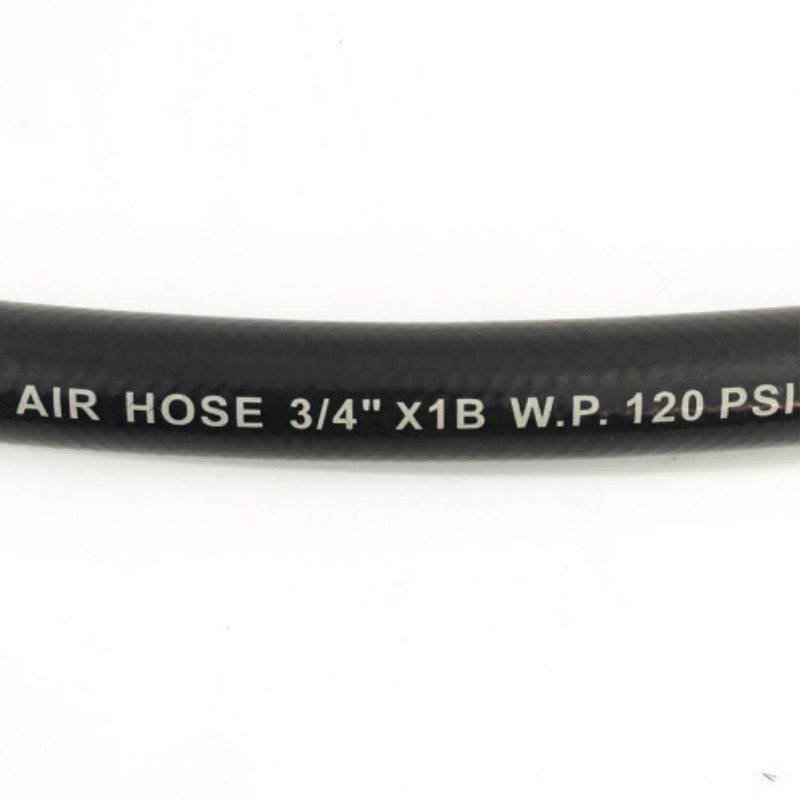
Temperature resilience is another area where braided rubber hoses excel. The rubber component naturally offers good thermal insulation, but when combined with high-quality braiding, it can also enhance the hose's ability to withstand both high and low temperature extremes. This makes them suitable for use in environments with fluctuating temperatures without experiencing degradation in performance.
When it comes to chemical resistance, braided rubber hoses are engineered to endure exposure to a wide range of substances. This characteristic makes them ideal for use in laboratories, chemical plants, and manufacturing facilities where exposure to corrosive or reactive substances might occur. Ensuring safe and secure transport of chemicals through a hose prevents potential leaks that could lead to both safety hazards and equipment damage.
braided rubber hose
Installation of braided rubber hoses is typically straightforward thanks to their flexibility and the availability of various connectors and attachments that make integration with existing systems seamless. For maintenance professionals, choosing the correct fittings and ensuring they are properly secured is vital for optimal performance and longevity of the hose systems.
From an environmental perspective, the longevity and robustness of braided rubber hoses contribute to reduced waste. High-quality hoses require less frequent replacement, meaning fewer resources are consumed in manufacturing and less material needs to be disposed of. This sustainability aspect appeals to both environmentally conscious industries and consumers, addressing growing demands for eco-friendly practices across various sectors.
In summary, braided rubber hoses represent a perfect synthesis of strength, flexibility, and durability. Their advanced construction ensures reliability in high-pressure environments, adaptability in confined spaces, and resilience across a range of temperatures and chemical exposures. Manufacturers and consumers alike benefit from their versatile applications and long-lasting performance, confirming their integral role in industrial and domestic scenarios. Whether in automotive applications, chemical transportation, or domestic plumbing, the value braided rubber hoses provide cannot be overstated, paving the way for safer and more efficient fluid management systems.
Understanding these elements from a supplier or engineer's perspective provides an authoritative and trustworthy source of information, emphasizing the expertise required to select the appropriate specifications for any given task involving braided rubber hoses.